Официальное открытие нового логистического центра в Людвигсбурге
В присутствии примерно 600 гостей состоялось торжественное открытие нового сервисно-логистического центра компании Lapp Group в Людвигсбурге, в честь которого было устроено ослепительное акробатическое шоу.
На сегодняшний день этот центр является одним из самых современных объектов такого типа, а запатентованные технологии транспортировки и автоматизированный высокий склад задают новые стандарты в данной области. «Мы инвестировали более 50 миллионов евро в наш новый сервисно-логистический центр – это самая большая сумма инвестиций в один объект за всю историю нашей компании, – говорит Андреас Лапп, председатель правления Lapp Holding AG. – Этот центр имеет огромное значение для наших заказчиков, наших сотрудников и для защиты окружающей среды, а также является значимой вехой на пути непрерывного развития нашей компании».
Открытие сервисно-логистического центра Lapp Group в промышленной зоне Хинтере Халден имеет также большое значение для развития города Людвигсбурга. «Я рад, что Lapp Group решила открыть свой центр в Людвигсбурге. Он повышает привлекательность нашего города как места ведения бизнеса, – говорит мэр города Вернер Спес. – Lapp является успешным транснациональным семейным предприятием нашего региона и компанией, придающей огромное значение высокому качеству и содействию устойчивому развитию. Поэтому мы так рады открытию сервисно-логистического центра компании в нашем городе. Приверженность Людвигсбурга устойчивому развитию города в последнее время привлекает большое внимание как на уровне страны, так и на международном уровне».
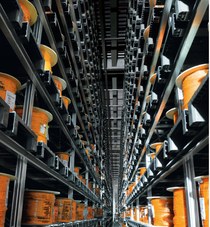
Удивительное здание
В новом сервисно-логистическом центре имеется три связанных между собой зала общей площадью 30 000 квадратных метров – это больше чем четыре футбольных поля – плюс офисное здание площадью 1 500 квадратных метров. Фасад имеет 270 метров в длину и 11 метров в высоту, 30 наклонных трапов для погрузки и разгрузки грузовых автомобилей. Центр построен в соответствии с последними руководящими указаниями касательно энергоэффективности. В системе отопления с верхней разводкой используются энергоэффективные трубчатые радиационные нагреватели, обеспечивающие среднюю температуру в 17–18 градусов. На крыше установлена фотоэлектрическая система, состоящая из 4 348 кристаллических модулей и способная вырабатывать до 1 000 МВт-ч ежегодно. Это означает, что 72 % потребляемой электроэнергии вырабатывается на месте в Людвигсбурге с использованием возобновляемых источников. Новый сервисно-логистический центр является полностью действующим с этой осени. До этого момента по одному выводились из эксплуатации ранее использовавшиеся склады в городе Фрайберг-на-Неккаре и городе Корнвестхайм. Некоторые из операций, которые ранее выполнялись в городе Форбах во Франции, теперь выполняются в Людвигсбурге. Строительные работы начались в 2011 году. На сегодняшний день в новом центре работает 130 человек, это на 45 человек больше, чем ранее работало на объектах во Фрайберге и Корнвестхайме вместе взятых. Ёмкость складских помещений также возросла примерно с 70 000 до 90 000 кабельных барабанов с соединительными и контрольными кабелями ÖLFLEX® и кабелями передачи данных UNITRONIC®.
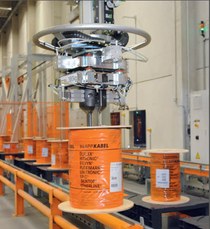
Инновационная технология
Основным новшеством в сервисно-логистическом центре является Зал 2, в котором может храниться до 74 000 кабельных барабанов диаметром от 400 до 800 миллиметров. Автопогрузчики с вильчатым захватом перевозят кабельные барабаны на конвейерную ленту длиной около 700 метров и шириной 600 миллиметров с четырьмя перегрузочными станциями. С этого момента весь процесс полностью автоматизирован благодаря двум инновациям, запатентованным компанией Lapp. Первая инновация представляет собой специальную захватную руку, известную под названием «штыревой захват». В центральное отверстие барабана вставляется штырь. Штырь затем раскрывается, что позволяет поднять барабан. Всего за один час одна из таких захватных рук может переместить, по крайней мере, 60 барабанов весом 400 кг каждый. «Использование этого метода позволяет нам избежать повреждений, которые иногда возможны при транспортировке маленьких барабанов автопогрузчиками с вильчатым захватом», – говорит исполнительный вице-президент Йозеф Хольц. Второй запатентованной инновацией стала специально разработанная система пластиковых поддонов. В поддонах предусмотрены выпуклости и желобки, позволяющие надежно зафиксировать барабаны для последующей транспортировки. Распределение продукции в пределах склада также полностью автоматизировано при помощи световых барьеров и технологии RFID. Транспортно-складские устройства помещают барабаны на соответствующие места на стеллажах и снимают их с многоярусных стеллажей, свободно перемещаясь по 18 проходам, что обеспечивает значительную экономию пространства. Раньше ширина проходов должна была составлять до 4 метров, чтобы по ним могли перемещаться погрузчики с вильчатым захватом, а теперь достаточно ширины в 1,20 метра.
Стандартный склад для поддонов находится в Зале 3, его емкость составляет около 17 000 кабельных барабанов диаметром 900 миллиметров и более. Автоматизированный склад бухт, который находится в Зале 1, обеспечивает еще 11 000 мест хранения.
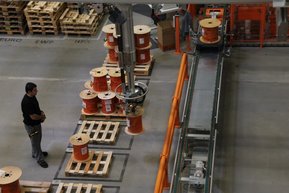
Модернизированная и ультрасовременная отгрузка
В Зале 1 осуществляется выполнение заказов, кабели нужной длины нарезаются, упаковываются и маркируются в соответствии с требованиями заказчика. Двенадцать транспортных систем для безлюдного производства транспортируют кабельные барабаны на станцию резки. Персонал, работающий на станции резки, может обрабатывать до 150 барабанов в день. Затем бухты или барабаны транспортируются при помощи конвейерной ленты к одной из пяти упаковочных станций. В совокупности эти станции могут готовить к отправке до 334 барабанов и 165 бухт в час.
Многочисленные преимущества
- Теперь можно осуществлять разовую поставку всей заказанной продукции в соответствии с требованиями конкретного заказа вместо отправки множества пакетов из разных мест. Результат: более сжатые сроки поставок.
- Новый сервисно-логистический центр также обладает значительными преимуществами для сотрудников, которые теперь могут работать в полностью обеспыленной среде. Все рабочие станции имеют эргономичный дизайн, сокращающий нагрузку на спину оператора.
- Принцип хранения всех кабельных барабанов в одном месте устраняет необходимость бессчетных перемещений по складу. Годовая экономия оценивается в 750 поездок грузовых автомобилей в год; а это, в свою очередь, означает годовое снижение выбросов CO2 примерно на 155 тонн.