The official opening of the new logistics center in Ludwigsburg
In the presence of about 600 guests, the grand opening of the new Lapp Group service and logistics center in Ludwigsburg took place, in honor of which a dazzling acrobatic show was staged.
Today, this center is one of the most modern facilities of this type, and patented transportation technologies and an automated high warehouse set new standards in this area. "We have invested more than 50 million euros in our new service and logistics center - this is the largest amount of investment in a single facility in the history of our company,– says Andreas Lapp, Chairman of the Board of Lapp Holding AG. "This center is of great importance for our customers, our employees and for environmental protection, and is also a significant milestone in the continuous development of our company."
The opening of the Lapp Group service and logistics center in the Hinter Halden industrial area is also of great importance for the development of the city of Ludwigsburg. "I am glad that Lapp Group has decided to open its center in Ludwigsburg. It increases the attractiveness of our city as a place of business," says Mayor Werner Spes. "Lapp is a successful multinational family enterprise in our region and a company that attaches great importance to high quality and the promotion of sustainable development. That is why we are so glad to open the company's service and logistics center in our city. Ludwigsburg's commitment to the sustainable development of the city has recently attracted a lot of attention both at the national and international levels."
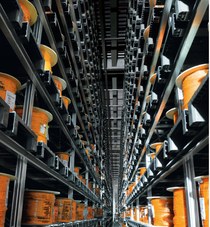
An amazing building
The new service and logistics center has three interconnected halls with a total area of 30,000 square meters - this is more than four football fields – plus an office building with an area of 1,500 square meters. The facade is 270 meters long and 11 meters high, with 30 inclined ramps for loading and unloading trucks. The center is built in accordance with the latest guidelines on energy efficiency. The overhead heating system uses energy-efficient tubular radiation heaters that provide an average temperature of 17-18 degrees. A photovoltaic system consisting of 4,348 crystal modules and capable of generating up to 1,000 MWh annually is installed on the roof. This means that 72% of the electricity consumed is generated locally in Ludwigsburg using renewable sources. The new service and logistics center has been fully operational since this fall. Up to this point, previously used warehouses in the city of Freiberg an der Neckar and the city of Kornwestheim were decommissioned one by one. Some of the operations that were previously performed in the city of Forbach in France are now performed in Ludwigsburg. Construction work began in 2011. To date, 130 people work in the new center, which is 45 more people than previously worked at the facilities in Freiberg and Kornwestheim combined. The storage capacity has also increased from about 70,000 to 90,000 cable drums with ÖLFLEX® connection and control cables and UNITRONIC® data cables.
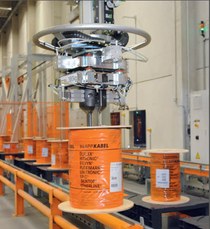
Innovative technology
The main innovation in the service and logistics center is Hall 2, which can store up to 74,000 cable drums with a diameter of 400 to 800 millimeters. Fork-lift trucks transport cable drums onto a conveyor belt about 700 meters long and 600 millimeters wide with four reloading stations. From now on, the entire process is fully automated thanks to two innovations patented by Lapp. The first innovation is a special gripping arm, known as a "pin grip". A pin is inserted into the central hole of the drum. The pin then opens, allowing the drum to be lifted. In just one hour, one of these gripping hands can move at least 60 reels weighing 400 kg each. "Using this method allows us to avoid damage that is sometimes possible when transporting small drums with fork–lift trucks," says Executive Vice President Josef Holtz. The second patented innovation was a specially designed plastic pallet system. The pallets have bulges and grooves that allow the drums to be securely fixed for subsequent transportation. The distribution of products within the warehouse is also fully automated using light barriers and RFID technology. The transport and storage devices place the drums in the appropriate places on the racks and remove them from the multi-tiered racks, moving freely through 18 aisles, which provides significant space savings. Previously, the width of the aisles had to be up to 4 meters so that fork-lift trucks could move along them, but now a width of 1.20 meters is enough.
The standard pallet warehouse is located in Hall 3, its capacity is about 17,000 cable drums with a diameter of 900 millimeters or more. The automated bay warehouse, which is located in Hall 1, provides 11,000 more storage locations.
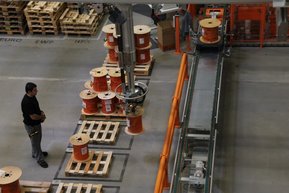
Upgraded and cutting-edge shipping
In Hall 1, orders are fulfilled, cables of the required length are cut, packaged and labeled in accordance with customer requirements. Twelve transport systems for unpopulated production transport cable drums to the cutting station. The staff working at the cutting station can process up to 150 drums per day. The coils or drums are then transported by a conveyor belt to one of the five packing stations. Together, these stations can prepare up to 334 drums and 165 coils per hour for shipment.
Numerous advantages
- Now it is possible to make a one-time delivery of all ordered products in accordance with the requirements of a specific order instead of sending multiple packages from different locations. The result: shorter delivery times.
- The new service and logistics center also has significant advantages for employees who can now work in a completely dust-free environment. All workstations have an ergonomic design that reduces the load on the operator's back.
- The principle of storing all cable drums in one place eliminates the need for countless movements around the warehouse. The annual savings are estimated at 750 truck trips per year; and this, in turn, means an annual reduction in CO2 emissions of about 155 tons.